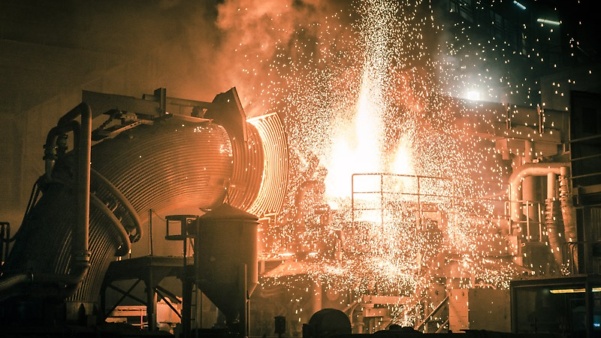
How our steel is produced: The electric steel plant.
The electric arc melts 135 t of scrap to molten steel.
The scrap arriving from the scrap yard is filled into the melting furnace by emptying both scrap baskets one after the other. The metallurgical experts call this process “charging the furnace“. After having retracted the electrode and opening the furnace lid the scrap basket is emptied into the vessel. Afterwards the lid is closed, the electrode enters and now the melting process is started. For that purpose an electric arc with an electrical power of up to 100 megawatt is ignited. In less than one hour the huge electric arc heats the scrap to a temperature of 1.620°C to produce molten steel.
The furnace vessel has a diameter of 6 m. The electric arc furnace is the core of our electric steel plant and functions according to the direct current electric arc principle. The furnace bottom serves as the anode. The electrode which brings the necessary energy into the furnace is made of graphite and has a diameter of 750 mm.
Our precisely controlled melting process.
During the melting of the steel many factors have to be harmonised with one another, such as, the electrode movement, the slag control, the carbon, sulphur and phosphor content as well as the flue gas temperature. This precision operation is monitored and controlled by our skilled staff from the control pulpit. The melting process is enhanced using laterally fixed natural gas burners and oxygen lances in the furnace. Undesirable substances which are generated during the melting of the scrap are retained in the slag floating on the surface of the molten steel. The flue gas of the melting process is extracted via an exhaust system to the modern flue gas cleaning equipment before leaving the plant.
The heat is optimized to comply with customer requirements.
A probe is used to automatically measure the temperature of the molten steel before tapping. Once the specified composition and temperature has been established the tapping process can begin. Just before tapping a preheated ladle is positioned underneath the furnace. The complete furnace vessel then tilts to pour the slag floating on the surface into a slag silo. The slag is later processed for recycling as building material and other uses. A final sample is taken from the furnace for analysis before tapping. The molten steel can then flow into the ladle of the transfer carriage. The transfer carriage travels a few meters from the electric arc furnace to the ladle furnace where a chemical analysis is carried out. The samples from the ladle are analysed in the laboratory next to the furnace platform. After a short wait the analyse-monitor displays the actual steel composition. Based on this analysis the properties are optimised by adding alloys and additives. The quality of the molten steel is also optimised so that the final product exactly complies with the customer specification. Further additives are added to the molten steel as necessary. Three 400 mm diameter electrodes ensure the correct transfer temperature. At the same time argon stirrers homogenise the molten steel. Once the parameters match the specifications the ladle transfer car travels into the casting shop.